Unveiling the Ins And Outs of Fasteners and Machining Procedures for Optimal Performance
In the realm of engineering and manufacturing, the choice of bolts and the details of machining processes play a pivotal role in identifying the supreme performance and sturdiness of an item. From the relatively simple job of picking the appropriate sort of fastener to the complex precision machining techniques utilized, every step in this process demands precise interest to information. As we start this expedition right into the globe of fasteners and machining, we will certainly discover the subtle yet crucial elements that can considerably affect the effectiveness and quality of the end product, dropping light on the frequently neglected facets that can make all the difference in accomplishing optimum performance.
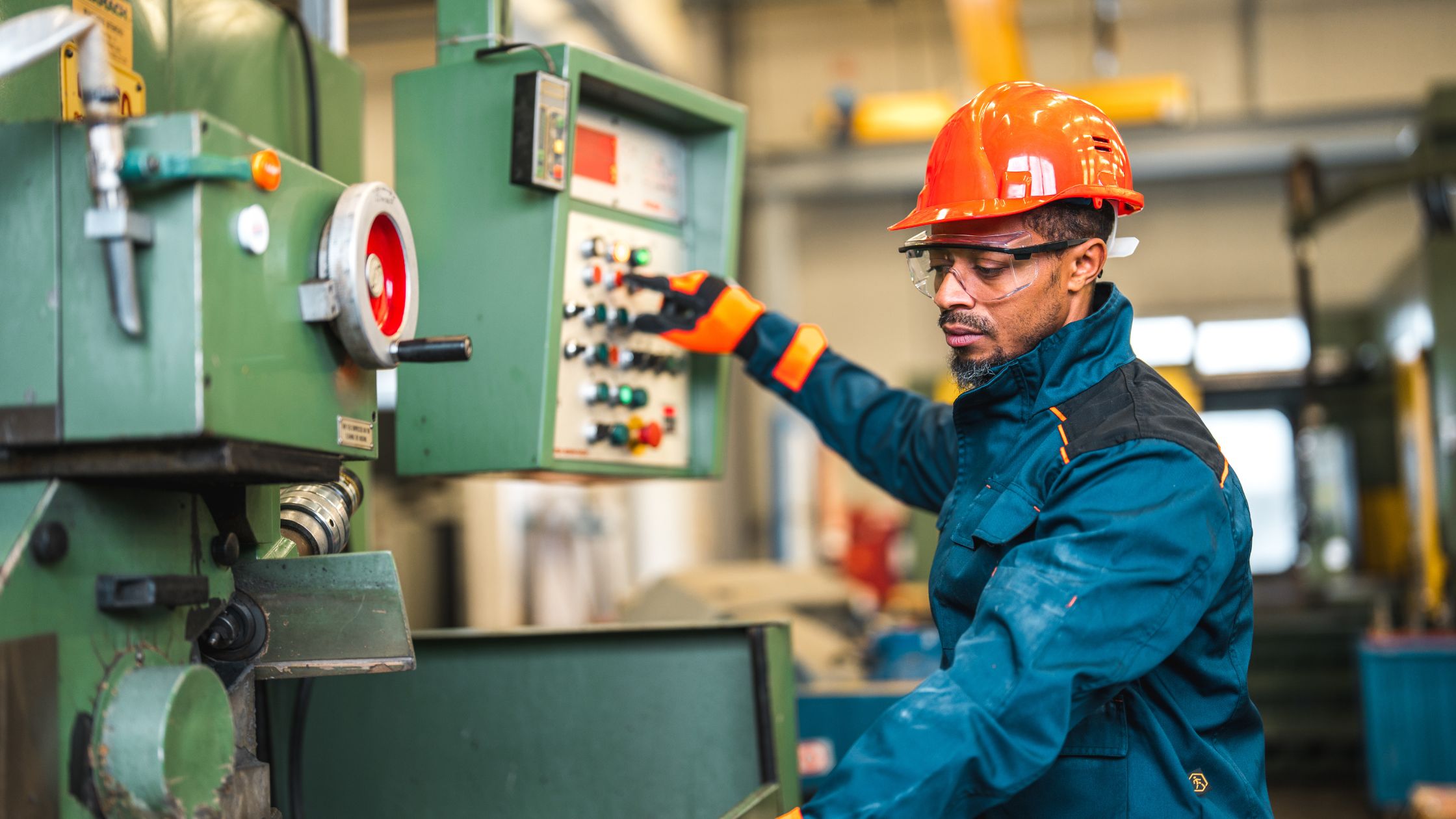
Value of Correct Bolt Choice
Picking the suitable bolts is essential in ensuring the structural integrity and longevity of any mechanical setting up. Bolts play a fundamental duty in holding components with each other firmly, with the ideal choice adding substantially to the total efficiency and reliability of the assembly. When picking fasteners, aspects such as product compatibility, environmental problems, load-bearing capacity, and simplicity of setup should be carefully taken into consideration to ensure optimal efficiency.
Inappropriate bolt option can bring about a variety of issues, including helping to loosen, deterioration, and even structural failure. Utilizing bolts that are not suited to the certain demands of the setting up can endanger its functionality and position safety and security threats. As a result, designers and designers need to carefully examine the application needs and select bolts that satisfy or go beyond the needed criteria and specs.
In addition, the right bolt selection process includes assessing the joint style, expected loads, vibration degrees, and prospective thermal expansion or tightening to ensure that the chosen fasteners can hold up against the operating problems properly. By focusing on proper fastener choice, producers can enhance the quality, resilience, and efficiency of their mechanical settings up.
Kinds and Characteristics of Bolts
An essential element of mechanical settings up lies in understanding the varied types and distinct characteristics of fasteners utilized in various commercial applications. Bolts are vital elements that hold structures with each other, making sure stability and capability. There is a vast array of bolts readily available, each made for details functions based upon the application requirements. Typical types of fasteners include screws, screws, nuts, pins, rivets, and washers.
Screws are threaded fasteners that are frequently made use of to sign up with 2 or even more components together. Screws resemble screws however are normally made use of with a nut to create a secure joint. Nuts are internally threaded bolts that mate with bolts to hold elements with each other. Washing machines are slim plates that disperse the load visit of a bolt, protecting against damages to the product being attached. Rivets are permanent fasteners that are hammered or pressed into place. Pins are utilized for alignment or to safeguard parts momentarily.
Comprehending the characteristics of each kind of bolt is crucial for choosing the ideal one for a certain application, ensuring ideal performance and dependability of the mechanical assembly. Fasteners and Machining.
Accuracy Machining Strategies for Performance
The detailed style requirements of numerous fasteners necessitate utilizing accuracy machining methods for ideal performance in producing processes. One of the main methods used in accuracy machining is Computer Numerical Control (CNC) machining, which makes it possible for high levels of precision and repeatability in the production of fasteners.
In addition to CNC machining, various other precision strategies such as grinding, milling, and transforming are frequently utilized to achieve the limited resistances needed for fasteners. These strategies permit suppliers to develop bolts with smooth surface areas, precise measurements, and high architectural honesty. By making use of accuracy machining strategies, suppliers can improve the high quality of bolts, lower material waste, and enhance general production efficiency. The use of advanced machining processes helps make sure click here for info that bolts meet market requirements and consumer expectations for performance and dependability.
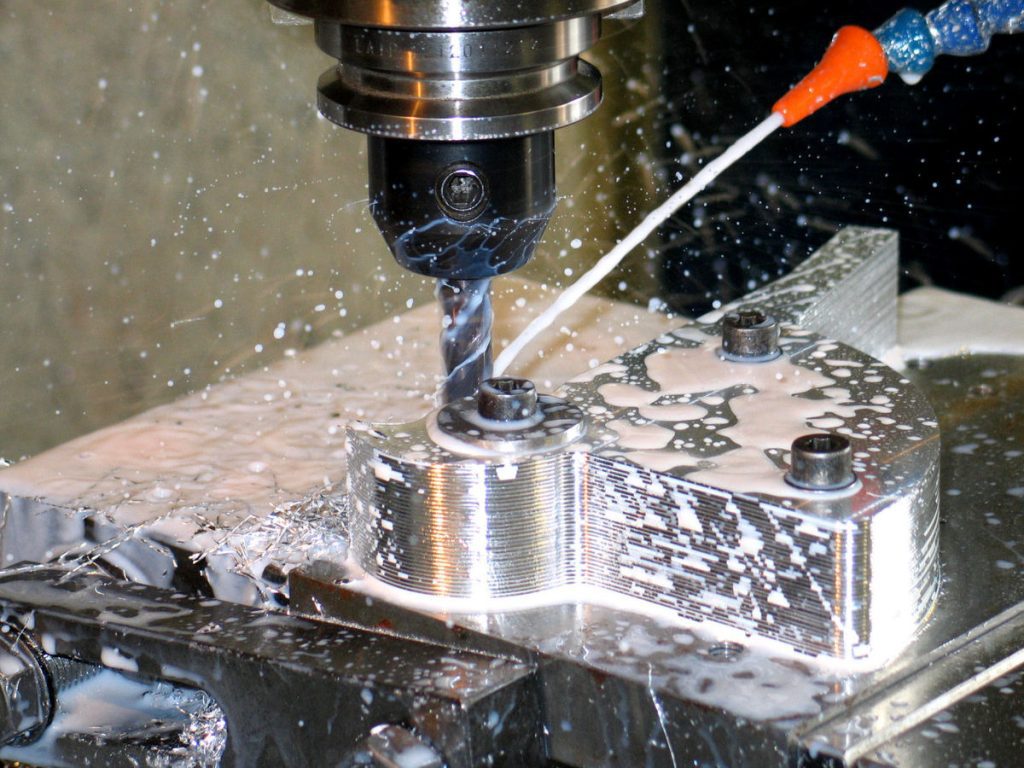
Aspects Affecting Machining Refine Performance
Numerous variables play a considerable role in figuring out the efficiency of machining procedures in the manufacturing of fasteners. Optimizing these specifications based on the particular requirements of the bolt being generated is key to accomplishing affordable and precise machining.
Machine rigidness and security additionally play an important role in establishing machining procedure efficiency. An experienced operator can make real-time changes, troubleshoot problems successfully, and make certain that the machining process runs smoothly, ultimately impacting the last quality of the bolt.

Quality Assurance Steps in Manufacturing
Aspects influencing machining procedure performance, such as cutting tool selection and maker stability, directly effect the implementation of quality assurance steps in production. Quality control measures are crucial in ensuring that products meet the called for specs and requirements. In the production process, numerous techniques are utilized to maintain top quality requirements. Assessment and screening play an important function in identifying any kind of discrepancies from the desired result. Normal upkeep of machining equipment is likewise essential to maintain quality assurance. Calibration of tools and devices is necessary to ensure accurate and specific production processes. In addition, carrying out standard operating treatments and procedures can aid in preserving consistency and high quality throughout the assembly line. Quality assurance gauges not only concentrate on the end item but additionally on every stage of the manufacturing process to avoid mistakes and problems. By adhering to rigid top quality control procedures, suppliers can enhance customer complete satisfaction, build a reputation for reliability, and inevitably achieve ideal efficiency in their machining procedures.
Conclusion
In verdict, picking the ideal bolts and utilizing precision machining techniques are crucial for ideal performance in manufacturing processes. check my reference Recognizing the types and features of bolts, along with aspects influencing machining process performance, can bring about improved efficiency and quality assurance measures. By taking note of these complexities, suppliers can attain greater degrees of performance and integrity in their items.
In the world of engineering and production, the choice of bolts and the details of machining processes play a pivotal duty in establishing the utmost performance and longevity of a product (Fasteners and Machining). One of the primary methods utilized in precision machining is Computer system Numerical Control (CNC) machining, which makes it possible for high degrees of precision and repeatability in the manufacturing of bolts. The usage of sophisticated machining processes aids make sure that bolts meet market requirements and client assumptions for performance and reliability
In verdict, choosing the ideal fasteners and using accuracy machining techniques are crucial for optimal efficiency in making processes. Understanding the kinds and features of fasteners, along with aspects affecting machining procedure performance, can lead to improved efficiency and quality control steps.